Building a Vinyl Seawall: Tips and Tricks for Success
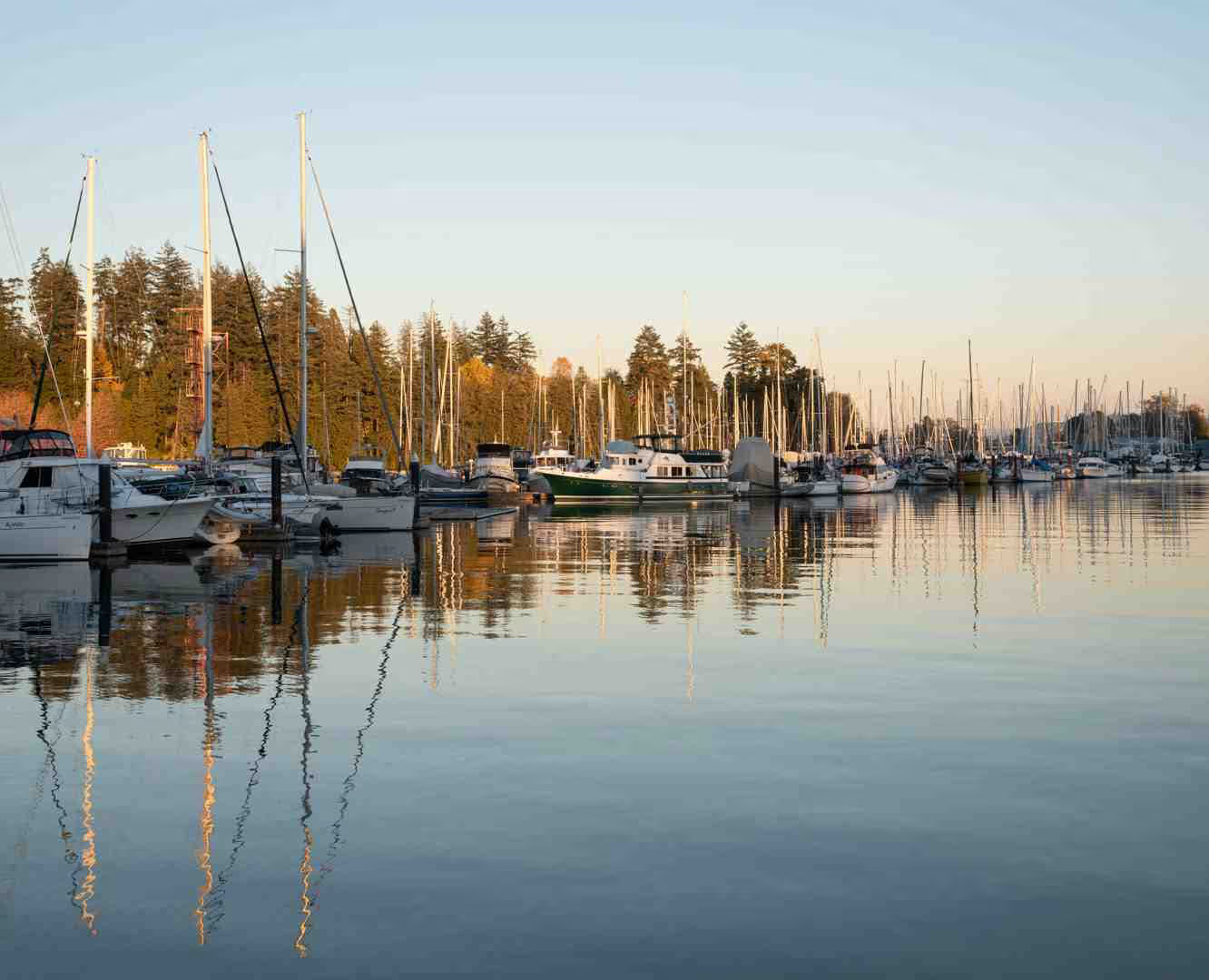
When it comes to vinyl seawall construction, homeowners and commercial property owners alike have much to gain from this innovative solution for shoreline protection. If you're interested in safeguarding your waterfront property from erosion and flooding, here's what vinyl seawalls offer:
- Durability: Built to withstand harsh weather and saltwater conditions, lasting 75+ years.
- Low Maintenance: Little upkeep is required compared to alternatives, ensuring peace of mind.
- Cost-Effective: Offers long-term savings with a worthwhile initial investment.
- Aesthetic Appeal: Available in various colors and styles to match your property's design.
Vinyl seawalls are made from polyvinyl chloride (PVC), a synthetic polymer that's resistant to corrosion and damage from saltwater. Unlike traditional materials like wood, steel, or concrete, vinyl is lightweight and strong, making it a preferred choice in regions like Florida. It's an advanced method that combines resilience with beauty, allowing property owners to protect their investments while enhancing the visual appeal of their surroundings.
Learn more about vinyl seawall construction:
What Is a Vinyl Seawall?
A vinyl seawall is a protective barrier built along shorelines to prevent erosion and flooding. It's made primarily from polyvinyl chloride (PVC), a durable synthetic material known for its resistance to harsh weather and saltwater. This makes vinyl seawalls a popular choice for homeowners looking to safeguard their waterfront properties.
Purpose and Benefits
The main purpose of a vinyl seawall is to protect land from being washed away by water. By acting as a sturdy barrier, it helps maintain the natural shape of the coastline and prevents costly damage to homes and businesses.
Vinyl seawalls are gaining popularity because they offer several advantages:
- Erosion Protection: They effectively prevent soil from slipping into the water, preserving valuable land.
- Flood Prevention: By blocking water, they reduce the risk of flooding during storms.
- Aesthetic Appeal: Available in various colors, they can complement any property design.
Materials and Construction
Vinyl seawalls are constructed using PVC, which is also found in everyday items like pipes and siding. This material is lightweight yet strong, making it ideal for withstanding the forces of nature without the need for heavy maintenance.
Vinyl Sheet Piling is a key component, providing a solid foundation. These sheets are stacked and driven into the ground, forming a robust base for the seawall. Tiebacks are used to reinforce the structure, ensuring it remains stable and secure.
Retaining Walls and Vinyl Caps add to the structural integrity and waterproofing, while Vinyl Bulkheads help contain debris and prevent erosion.
By choosing a vinyl seawall, property owners benefit from a long-lasting solution that combines functionality with visual appeal. It's an investment that not only protects but also improves the value of waterfront properties.
Components of Vinyl Seawall Construction
A successful vinyl seawall construction involves various components working together to create a robust and durable barrier. Here's a look at each part and its role in the overall structure:
Vinyl Sheet Piling
Vinyl sheet piling forms the backbone of a vinyl seawall. These sheets are driven deep into the ground to create a solid foundation. Typically, the piling should extend at least 3 feet below the surface. This ensures stability and prevents water from seeping in. The sheets can be cut to fit any project specifications, making them versatile for different landscape needs.
Tiebacks
Tiebacks are crucial for reinforcing the seawall. These long steel bars run perpendicular to the wall, adding strength and preventing gaps or cracks. By anchoring the wall to the ground, tiebacks maintain the structural integrity of the seawall, ensuring it withstands erosion and pressure from water.
Retaining Walls
Retaining walls are vital for soil maintenance. They prevent soil from slumping or eroding, especially in areas with uneven terrain. Installed along the outer edges of the property, retaining walls help maintain the land's natural shape and support the overall seawall structure.
Vinyl Caps
Vinyl caps serve as a waterproof barrier atop each panel. They provide a smooth finish and protect the seawall from moisture intrusion. Available in various shapes and sizes, these caps can be custom to withstand different levels of saltwater erosion and weight pressure.
Vinyl Bulkhead
Vinyl bulkheads are installed perpendicularly to the shoreline. They play a key role in erosion prevention and debris containment. Acting as a primary barrier, bulkheads stop water from wearing away the coastline and can also support structures like docks or decks.
Drainage Systems
Proper drainage systems are essential for flood prevention and stormwater management. They help direct water away from the seawall, reducing pressure and preventing potential damage during heavy rainfall or storms. Efficient drainage systems ensure the longevity and effectiveness of the seawall.
By integrating these components, a vinyl seawall offers a comprehensive solution for protecting waterfront properties. Each element works in harmony to provide a strong, low-maintenance, and aesthetically pleasing barrier against the forces of nature.
Benefits of Vinyl Seawalls
When it comes to protecting your waterfront property, vinyl seawall construction offers numerous benefits that make it a standout choice. Let's explore why vinyl seawalls are gaining popularity among homeowners and property developers.
Durability and Longevity
Vinyl seawalls are known for their exceptional durability. They are designed to withstand harsh weather conditions, including intense sunlight, strong tides, and direct hit hurricanes. The material's resilience to UV rays ensures that the seawall maintains its integrity and appearance over time. Additionally, vinyl is resistant to marine borers, which can be a significant problem for wooden seawalls. This resistance to both natural elements and marine life contributes to a longer lifespan, often exceeding 20 years with proper inspection and maintenance.
Cost-Effectiveness
One of the most appealing aspects of vinyl seawalls is their cost-effectiveness. The initial investment is typically lower compared to concrete or steel seawalls because vinyl does not require heavy-duty equipment for installation. Over the long term, vinyl seawalls offer savings through reduced maintenance costs and potential increases in property value. With minimal repairs needed, property owners can enjoy peace of mind knowing their seawall is both a smart financial and protective investment.
Aesthetic Appeal
Vinyl seawalls also score high on aesthetic appeal. They come in various colors and styles, allowing for customization that matches the surrounding landscape and personal preferences. This design flexibility means that vinyl seawalls can seamlessly blend with or improve the look of a property. Whether you prefer a natural look or a more modern design, vinyl allows for creative expression without compromising on function.
Low Maintenance
Another significant advantage of vinyl seawalls is their low maintenance requirements. Once installed, they require very little upkeep. The protective vinyl sheets seal in the concrete and steel rebar, minimizing exposure to the elements and reducing the need for frequent repairs. This ease of maintenance is a critical factor for many property owners, as it saves both time and money in the long run.
In summary, vinyl seawalls offer a perfect blend of durability, cost-effectiveness, aesthetic appeal, and low maintenance. These benefits make them an excellent choice for anyone looking to protect their waterfront property with a reliable and attractive barrier.
Let's explore the construction process of vinyl seawalls, from planning to installation steps and inspection routines.
Vinyl Seawall Construction Process
Building a vinyl seawall involves several key steps, each crucial for ensuring the structure's effectiveness and longevity. Let's break down the process into planning, installation, and maintenance.
Planning and Permits
Before you break ground, careful planning is essential. This involves a site assessment to understand the topography, soil conditions, and local water dynamics. Knowing these factors helps in designing a seawall that fits the specific needs of your property.
Next, you'll need to steer regulatory requirements. Securing the necessary permits can take time, often 9-12 months, so starting early is crucial. Work with professionals who are familiar with local regulations to streamline this process and avoid delays.
Installation Steps
Once planning is complete and permits are secured, the construction phase begins. Here's a step-by-step guide to the installation process:
Preparation: Clear the site of any debris and stabilize the ground. This ensures a solid foundation for your seawall.
Sheet Piling: Install the vinyl sheet piling, which forms the backbone of the seawall. These sheets are driven deep into the ground to provide stability and protect against erosion.
Tiebacks: Reinforce the seawall with tiebacks. These steel bars add structural integrity, preventing cracks and maintaining the wall's strength over time.
Capping: Add vinyl caps to the top of the wall. These caps create a smooth finish and act as a waterproof barrier, protecting the wall from moisture damage.
Drainage: Implement drainage systems to manage stormwater and prevent flooding. Proper drainage is essential for maintaining the seawall's integrity and preventing water buildup.
Inspection and Maintenance
Routine maintenance is key to ensuring your seawall lasts for decades. Here are some tips for keeping it in top shape:
Routine Checks: Regularly inspect the seawall for signs of wear or damage. Look for cracks, loose tiebacks, or erosion around the base.
Post-Storm Inspections: After severe weather events, conduct thorough inspections to assess any damage. Addressing issues promptly can prevent minor problems from escalating.
By following these steps, you can build and maintain a vinyl seawall that effectively protects your property from erosion and flooding. This proactive approach ensures your investment remains sound and your waterfront remains secure.
Next, let's address some frequently asked questions about vinyl seawalls to help you make informed decisions.
Frequently Asked Questions about Vinyl Seawalls
Are Vinyl Seawalls Good?
Yes, vinyl seawalls are a fantastic choice for many property owners. They offer a combination of durability, low maintenance, and cost-effectiveness that makes them stand out. Vinyl is a robust material that can withstand harsh weather conditions, including heavy rains and high tides, without deteriorating. This makes it ideal for long-term use in marine environments.
Moreover, vinyl seawalls require minimal upkeep compared to other materials like wood or concrete. This low maintenance aspect saves both time and money over the years. Homeowners can enjoy peace of mind knowing their seawall will remain intact and functional with little intervention.
How Much Does a Vinyl Seawall Cost?
The cost of a vinyl seawall can vary based on several factors. Here are the key considerations:
Property Size: Larger properties require more materials and labor, increasing the overall cost.
Material Type: Different types of vinyl offer varying levels of durability and weather resistance. Choosing a higher-quality material might be more expensive upfront but can provide better longevity.
Additional Features: Adding features like lighting, benches, or railings can improve the seawall's functionality and appearance but will also raise the cost.
Soil Conditions: If your property has rocky or clay-heavy soil, the installation might require more labor, thus increasing the cost.
It's important to consult with a marine contractor to get an accurate estimate custom to your specific needs and location.
Do Vinyl Seawalls Need Weep Holes?
Yes, weep holes are an essential component of vinyl seawall construction. They play a crucial role in pressure release and drainage. Weep holes allow water to escape from behind the seawall, reducing the pressure on the structure. This helps prevent potential damage and prolongs the seawall's lifespan.
Proper drainage is vital to maintaining the integrity of the seawall. Without weep holes, water buildup can lead to increased pressure and potential structural failure. Including them in your design ensures that your seawall remains effective in protecting your property from flooding and erosion.
Understanding these aspects of vinyl seawalls can help you make informed decisions about your property protection. In the next section, we'll wrap up with a summary and provide contact information for Pearce Marine Construction.
Conclusion
In summary, vinyl seawalls offer a robust, low-maintenance, and cost-effective solution for protecting waterfront properties. Their durability against harsh weather conditions, resistance to UV rays, and immunity to marine borers make them a top choice for long-term shoreline protection. Additionally, the aesthetic flexibility and minimal upkeep requirements further improve their appeal.
At Pearce Marine Construction, we bring generational expertise and meticulous craftsmanship to every project. As a woman-owned marine construction company in Long Island, NY, we specialize in building and maintaining bulkheads, docks, decks, and other shoreline protection structures. Our team is dedicated to delivering high-quality solutions custom to your needs, ensuring your property is well-protected and aesthetically pleasing.
If you're considering a vinyl seawall for your property or need more information, we invite you to explore our services or reach out to us directly. Our experts are ready to assist you with your marine construction needs, providing guidance and support every step of the way.
For inquiries, consultations, or to start your project, please contact us. We're here to help you safeguard your property with the best in marine construction.
Contact Us
Corporate Office
Massapequa Park, NY 11762