From Shore to Structure: Mastering Concrete Sea Wall Construction
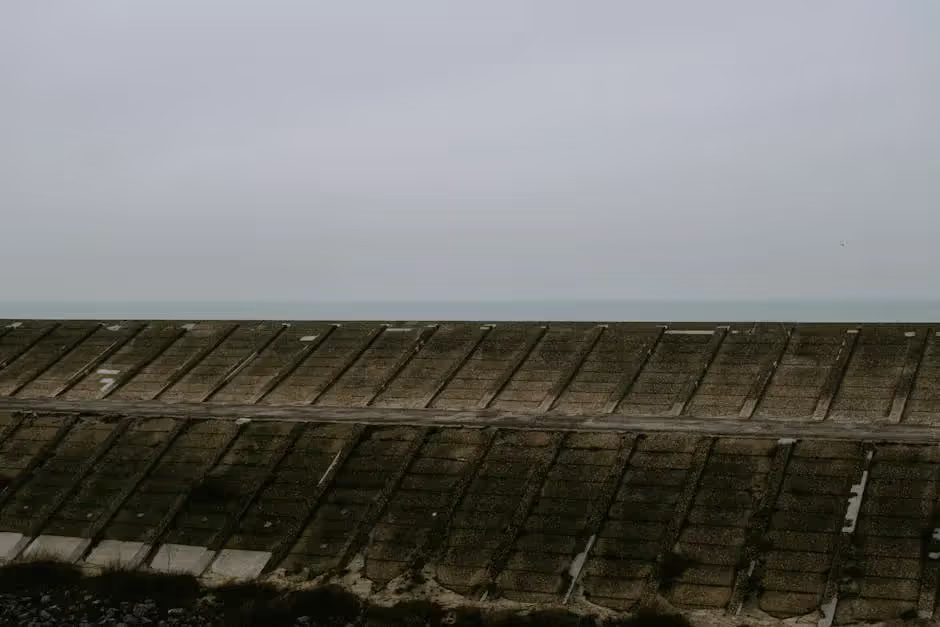
Concrete sea wall construction is a robust solution to safeguarding properties from the persistent threats of land erosion and storm surges that plague waterfront locations. Whether you own a home nestled along the shores of Long Island or manage a commercial property, understanding the essence of concrete sea wall construction is key to ensuring lasting shoreline protection. Here's what you need to know:
- Land Erosion: Concrete sea walls are engineered to prevent soil loss caused by waves and tides, securing your property line over time.
- Storm Surges: These barriers act as a vital shield against high seas and extreme weather, mitigating the risk of flooding.
- Shoreline Protection: By absorbing and deflecting wave energy, concrete sea walls help maintain the natural contour of your shoreline, preventing damage and loss of land.
In the dynamic environment of Suffolk and Nassau Counties, and all the picturesque locales of Long Island, the need for reliable sea wall construction has never been more pressing. As coastal communities face more frequent and severe weather, these sturdy structures offer an essential defense, preserving both the land and its value.
Understanding Concrete Sea Wall Construction
Building concrete sea walls is an art and a science. These structures must stand strong against the relentless forces of nature. Let's explore the key components and construction process that make these walls so effective.
Key Components
Concrete Panels
At the heart of any concrete sea wall are the panels. These are large, precast sections made from high-density concrete. They offer best durability and are designed to withstand the harsh conditions of coastal environments. The panels are often twice as dense as standard requirements, ensuring they last longer and provide superior protection.
Reinforcing Steel (Rebar)
Rebar is crucial for adding strength to concrete sea walls. This steel reinforcement helps the wall resist tension forces, preventing cracks and ensuring the structure remains intact even under heavy wave action. It's often coated with epoxy to prevent rust, enhancing the wall's longevity.
Seawall Cap
The seawall cap ties everything together. It's poured onsite and reinforced with custom stirrup-shaped rebar, providing additional structural support. This cap not only adds to the stability of the wall but also ensures a neat finish, protecting the top edges from erosion.
Construction Process
Precast Panels
The use of precast panels speeds up the construction process. These panels are produced in a controlled environment, ensuring quality and consistency. Once on site, they can be quickly installed, reducing the time needed for construction and minimizing disruptions.
Installation Techniques
Installing a concrete sea wall involves precise techniques. Panels are not hammered into place but are jetted in by churning up the sand. This method ensures the panels penetrate deeply into the canal bed, providing a solid foundation.
Deadman Anchors
To keep the wall stable, deadman anchors are installed every 10 feet. These anchors extend back about 15 feet into the ground, holding the wall firmly from the landward side. Made from epoxy-coated rebar, they are covered in a poly pipe sleeve to prevent rusting, ensuring they remain effective over time.
Concrete sea wall construction is a meticulous process, requiring expertise and attention to detail. Each component plays a vital role in creating a barrier that not only protects but also stands the test of time. As we explore further, we'll compare these robust structures to their vinyl counterparts, highlighting the unique benefits each offers.
Comparing Concrete and Vinyl Seawalls
When it comes to protecting your shoreline, choosing the right type of seawall is crucial. Both concrete and vinyl seawalls have their own set of advantages, and understanding these can help you make an informed decision.
Concrete Seawalls
Durability and Strength
Concrete seawalls are known for their durability. With proper maintenance, they can last over 30 years. The key to their strength lies in the reinforcing steel, or rebar, embedded within the concrete. This steel reinforcement helps resist tension forces, preventing cracks and maintaining the wall's integrity even under heavy wave action.
Maintenance
Despite their strength, concrete seawalls require regular maintenance. Exposure to saltwater can lead to cracks, allowing water to reach the rebar and cause rust. Regular inspections and timely repairs are essential to prolong the lifespan of these structures.
Lifespan
While concrete seawalls have a substantial lifespan, they often need more frequent repairs compared to vinyl. However, with ongoing care, they remain a robust choice for many waterfront properties.
Vinyl Seawalls
Aesthetics and Longevity
Vinyl seawalls offer a sleek, modern look and can last over 50 years. Unlike concrete, vinyl doesn't rust, crack, or rot, making it a low-maintenance option. This makes vinyl an attractive choice for those seeking a long-lasting, visually appealing solution.
Installation
Vinyl seawalls are easier to install than their concrete counterparts. They are lightweight, requiring less heavy machinery, which minimizes yard disruption. This ease of installation can be a significant advantage in areas with limited space for construction equipment.
Hybrid Seawalls
For those seeking the best of both worlds, hybrid seawalls like Truline offer a compelling option. These combine the strength of steel-reinforced concrete with the longevity of vinyl. Truline's innovative design includes dual-interlocking forms that create a closed cell for pouring concrete, allowing installation in various soil conditions, including rocky areas.
Each type of seawall—concrete, vinyl, or hybrid—has its own strengths. Your choice will depend on factors like location, soil type, and specific needs. Understanding these differences ensures you select a seawall that provides the best protection for your property.
Cost and Maintenance Considerations
When considering concrete seawall construction, understanding the costs and maintenance involved is crucial. Let's explore the key factors that impact your investment and how you can ensure your seawall stands the test of time.
Cost Factors
Material Costs
Concrete seawalls primarily consist of concrete panels and reinforcing steel (rebar). While concrete is a durable choice, it can be more expensive than other materials like wood or vinyl. The cost of materials will vary based on quality, thickness, and the specific design requirements of your seawall.
Labor
Labor is a significant part of the overall cost. Installing a concrete seawall involves skilled workers who can handle tasks like jetting panels into the canal bed and ensuring proper alignment. Labor costs can range widely based on the complexity of the project and local labor rates.
Geographical Location
Your location plays a big role in determining costs. Areas prone to erosion or high wave activity might require more robust designs, increasing both material and labor costs. Additionally, local regulations and permit requirements can add to the overall expense.
Construction Cost Overview
On average, building a concrete seawall can cost between $150 and $450 per linear foot. This range depends on factors like design complexity, location, and the need for additional features like deadman anchors.
Maintenance Tips
Regular Inspections
To maintain the integrity of your concrete seawall, regular inspections are vital. Check for signs of wear, such as cracks or separation at the joints. Early detection of issues can prevent costly repairs down the line.
Repair Cracks
Concrete is strong, but it can develop cracks over time, especially when exposed to saltwater. It's essential to repair any cracks promptly to prevent water from reaching the rebar, which can lead to rust and compromise the wall's strength.
Protect Steel
The rebar within the concrete is crucial for maintaining structural integrity. Protecting it from rust is key. Use epoxy-coated rebar or apply protective sealants to prevent moisture from causing corrosion.
Lifespan and Longevity
With proper maintenance, a concrete seawall can last over 30 years. Regular care ensures the wall remains a formidable barrier against erosion and storm surges, safeguarding your property for decades.
By keeping these cost and maintenance considerations in mind, you can make informed decisions that protect your investment and ensure your seawall remains effective for years to come.
Frequently Asked Questions about Concrete Sea Wall Construction
How long does a concrete sea wall last?
A well-built concrete sea wall can last over 30 years, providing robust protection against erosion and storm surges. The key to achieving this lifespan lies in regular maintenance and timely repairs. By addressing minor issues like cracks early, you can prevent them from escalating into major problems that could significantly shorten the seawall's life.
How thick should a concrete sea wall be?
The thickness of a concrete sea wall is crucial for its structural integrity. Typically, concrete panels used in seawall construction are designed with a thickness that can withstand the forces of strong waves and heavy boat traffic. Pearce Marine Construction often recommends panels with a minimum thickness that aligns with local regulations and site-specific needs. This ensures the wall can effectively resist the pressure and movement of water.
How much does a concrete sea wall cost?
The cost of constructing a concrete sea wall can vary widely. On average, you might expect to pay between $150 and $450 per linear foot. Several factors influence this range, including:
- Material Costs: The choice of high-quality concrete and rebar can increase costs but also improve durability.
- Labor: Skilled labor is essential for proper installation, impacting overall expenses.
- Geographical Location: Areas with high erosion risk or strict building codes may require more complex and costly designs.
Understanding these factors will help you budget effectively and ensure your seawall provides lasting protection for your property.
Conclusion
At Pearce Marine Construction, we pride ourselves on our generational expertise and meticulous craftsmanship in concrete sea wall construction. With years of experience serving Nassau and Suffolk County, our family-owned business has built a reputation for delivering high-quality marine construction solutions that stand the test of time.
Our team understands that a well-constructed seawall is vital for protecting your property from erosion and storm surges. That's why we focus on using the best materials and techniques available. Our concrete panels are carefully designed to meet local regulations and withstand the harshest conditions, ensuring durability and strength.
We also believe in the importance of regular maintenance and timely repairs to extend the lifespan of your seawall. Our skilled professionals are trained to spot potential issues early and address them before they become major problems. This proactive approach helps keep your seawall in top condition and maximizes its protective benefits.
Choosing Pearce Marine Construction means choosing a partner committed to quality and customer satisfaction. Our attention to detail and dedication to excellence ensure that your seawall not only meets but exceeds your expectations.
For more information about our services, visit our Seawalls and Bulkheads page and find how our expertise can safeguard your waterfront property.
Contact Us
Corporate Office
Massapequa Park, NY 11762